Metal casting is an ancient process used to create a variety of objects from intricate sculptures to everyday household items. For centuries, metal casters have sought ways to achieve precision in their craft, employing the use of molds as one way of doing so.
In this article we will explore the role molds play in achieving precision in metal casting, examining how these tools can help produce components with accurate dimensions and shapes. We will also discuss some common methods of mold creation and how they are best utilized when crafting specific objects.
Finally, we will look at the importance of quality control procedures when using molds for metal casting projects.
The Benefits of Mold Design and Manufacturing in Metal Casting
Mold design and manufacturing are an important part of achieving precision in metal casting. Having a well-designed and high-quality mold can help create consistent and accurate parts that meet the exact specifications of the product.
With precise molds, there are many benefits to be gained from using them for metal casting production. One benefit is that molds allow manufacturers to produce higher quality products with greater efficiency than traditional methods.
Because they are designed to provide repeatable accuracy over multiple batches of production, they save time and money by reducing scrap rates due to imperfections or incorrect dimensions in castings. Additionally, this level of precision ensures more reliable products with fewer defects while providing faster turnaround times for customers.
Another advantage is that custom molds offer increased flexibility in terms of size and shape as well as allowing for intricate details not possible through other processes such as die casting or sand casting. This makes it easier to create complex shapes without sacrificing strength or accuracy which can translate into cost savings when producing large orders or unique pieces with detailed features required for certain applications.
Finally, mold design and manufacturing also eliminate any concerns about safety issues associated with traditional methods like hand carving since tooling will remain consistent throughout each batch run resulting in reduced risk of injury or accidents on the factory floor. In addition, proper maintenance procedures will ensure longer life spans leading to further cost savings over time due to lower replacement costs compared to other techniques used in metal casting operations
Understanding the Necessity of Molds for Precision Casting
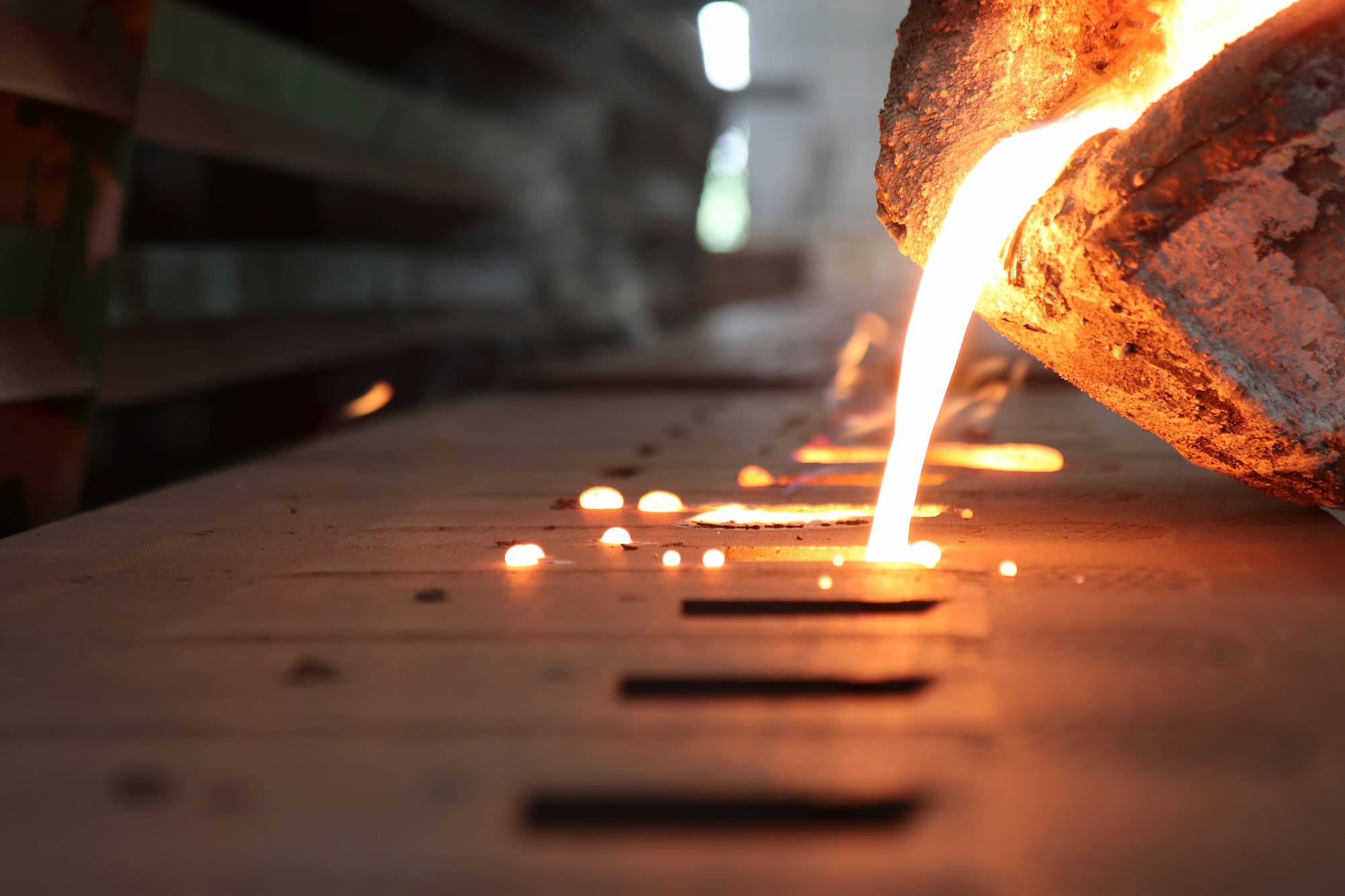
To achieve precision in metal casting, the use of molds is essential. Molds provide a template for the molten metal which ensures that it takes on a desired shape and size.
Without them, achieving high levels of accuracy would be impossible. The design of the mold will depend upon what type of product is being cast and its specific needs.
For example, complex shapes may require more intricate designs while simpler forms may only need basic outlines. It is also important to consider how easily removable the mold should be from the final product and whether any additional features are required such as venting holes or channels for air circulation when pouring in liquid metal.
By understanding these requirements, manufacturers can create molds that are suited to their particular casting project needs, ensuring greater accuracy and consistency with each pour.
Implementing Quality Control Measures Through Proper Mold Design
Molds are essential for achieving precision in metal casting, and proper mold design is key to implementing quality control measures. From the shape of the finished product to its consistency and accuracy, molds play a major role in producing high-quality results.
For example, when designing a mold, engineers must consider factors such as strength requirements, surface finish needs, and formability. Additionally, they must also take into account any potential problems that could arise during production or while using the finished product.
By considering all these elements ahead of time through proper design techniques, manufacturers can ensure quality products with minimal waste or defects. Furthermore, by carefully testing each step of the process – from material selection to assembly – companies can be assured that their result adheres to all industry standards for safety and performance.
Ultimately, this allows them to deliver consistent results at lower costs than would otherwise be possible without utilizing proper molds and ensuring quality control measures through careful design planning.
Exploring the Role of Advanced Technology in Creating Perfectly-Fitted Molds

Advanced technology has revolutionized the process of creating perfectly fitted molds for metal casting. With 3D printing, engineers can now create highly intricate and precise shapes that were not possible before. Computer-aided design (CAD) allows users to input all necessary dimensions into a system and generate a perfect mold in minutes. Automated milling machines are also available which take raw material pieces and shape them with high precision according to the designer’s specifications.
Using these advanced technologies, manufacturers can achieve accuracy down to the micron level in their molds, ensuring that each part is exactly as planned when it comes time for casting. Additionally, robotics have been introduced into many factories so that automation processes such as automated assembly become faster and more efficient than ever before.
All these new technologies make it easier for manufacturers to produce perfectly fitted molds quickly while still maintaining high levels of quality control throughout the entire production process.
Conclusion
Metal Casting is an essential process to achieve precision in many industries, and molds play a major role in this. By providing structure and shape, molds are used to form the molten metal into its desired shape with accuracy, allowing for complex parts that could not be made any other way.
Molds are also critical for achieving repeatability; when the same mold is used over multiple castings, they will come out looking nearly identical each time. This consistent quality control makes it possible to produce large quantities of items with uniformity and predictability, saving companies money while ensuring optimal performance from their products.
