Laser cutting is a complex art and science that has been used for decades to bring ideas from concept to finished product. It requires accuracy, precision, and skill to produce the desired results.
In recent years laser cutting technology has advanced significantly, making it easier than ever before to create intricate designs with incredible detail. This article will explore the history of laser cutting and how it come to be such a powerful tool today, as well as provide an overview of the various techniques involved in taking a concept through production.
Well, look at what goes into selecting materials for your project, understanding different types of lasers and their capabilities, learning proper safety protocols when operating machinery, and finally see how these pieces come together in creating something truly unique. Join us on this journey as we gain insight into the artistry and science behind laser cutting!
Introduction to Laser Cutting Technology
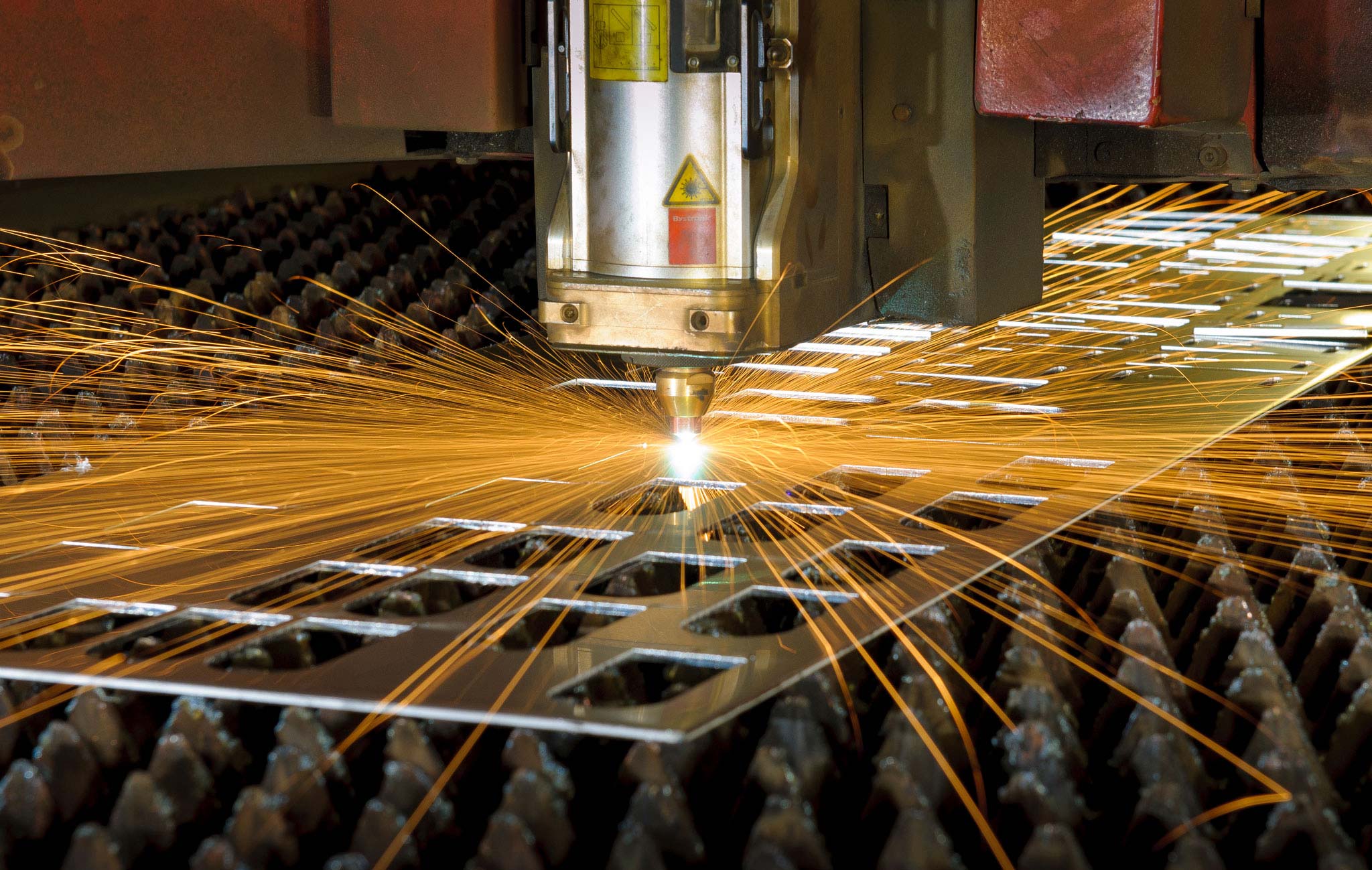
Laser-cutting technology has revolutionized the way we create artwork and products. It is an invaluable tool for professionals in manufacturing, engineering, design, and art fields alike.
The process of laser cutting involves using a focused beam of light to cut or engrave materials such as wood, metal, plastic, glass, stone, and more. With its highly precise results and minimal waste material production, it can be used to craft intricate objects with incredible accuracy.
This article will explore the fundamentals behind laser cutting from concept creation to finished product; including its advantages over traditional methods as well as some tips on how to get started with this exciting technology.
Understanding the Process of Laser Cutting
When it comes to laser cutting, the process can be broken down into multiple steps. From the initial concept to the final product, each step needs careful consideration.
First, the material that will be used for laser cutting must be chosen. The laser beam interacts differently with different materials like plastics or metals and so depending on what is being made, this should form part of the planning process.
Next, a CAD program is often employed to create an accurate vector illustration of the design before it’s sent for production. This provides a blueprint that informs where on the sheet metal or plastic will need to be cut by the machine.
The third stage involves setting up and running the machine itself to begin producing parts from your design files as accurately as possible according to specifications provided in steps one and two respectively. Special attention must also be paid throughout this stage regarding material waste produced during manufacturing—the goal here is always efficiency! Finally, once all components have been cut they then undergo some finishing touches such as sanding or drilling if needed before piecing them together into their finished product form – ready for use!
Exploring the Design Possibilities of Laser Cutting
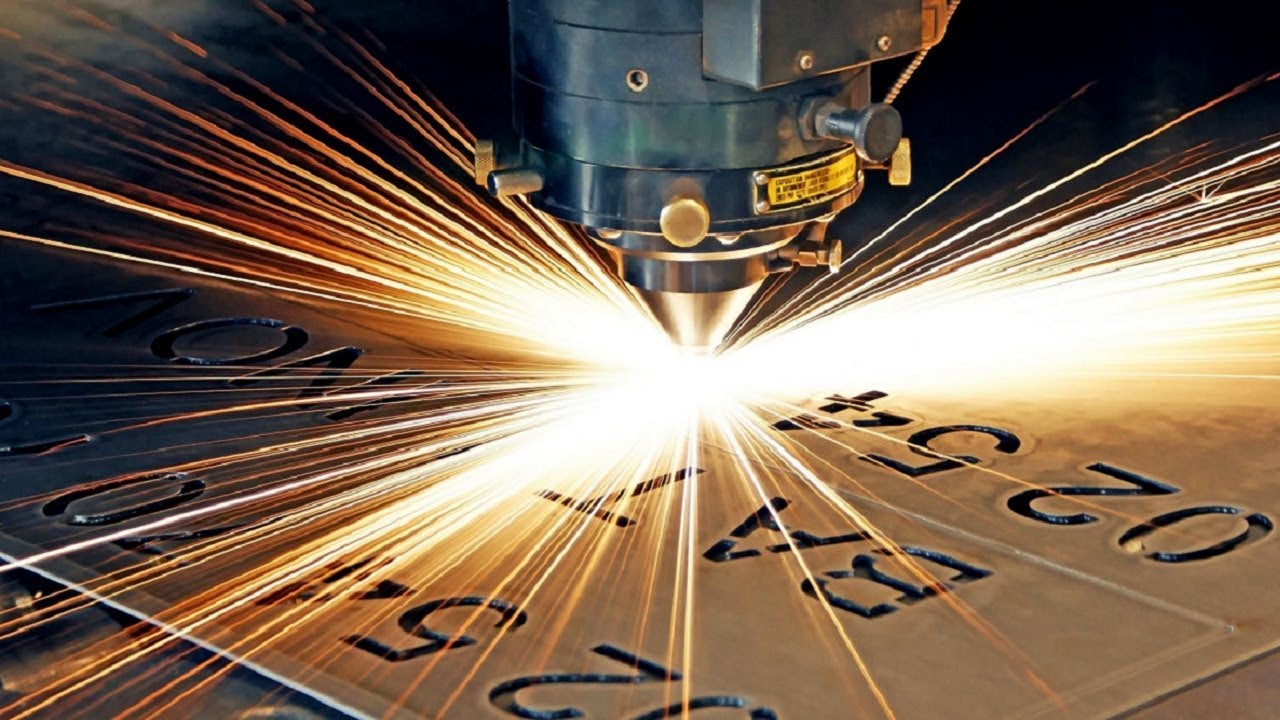
Creating with laser cutting technology has opened up a world of possibilities for designers and makers. From intricate engravings to detailed cutouts, the technology enables us to explore entirely new design processes that were not possible before.
With its ability to turn almost any material into a workable canvas, it is no wonder why laser cutting is so popular among craftspeople and hobbyists alike. It offers an unparalleled degree of precision that can be used to create complex shapes and patterns in just about any material imaginable.
The use of laser cutting also allows for a greater range of customization than ever before when creating products. By taking advantage of the different settings available on laser machines, users have the freedom to customize their designs down to even the most minute details such as size, shape, or texture – all at an incredibly fast rate compared to other methods such as hand-cutting or 3D printing. What’s more, because each item produced through this process is unique due to its complexity and customizability options available with lasers – one could say there are virtually limitless design possibilities when it comes to working with this type of machinery! From small trinkets made from wood or metal right to large-scale projects crafted out of acrylics or plastics – anything truly seems achievable with modern-day laser cutters!
Conclusion
Laser-cutting technology has revolutionized the way materials are manipulated and shaped into products. It is a precise tool that allows for intricate designs while still being cost-effective.
The art and science of laser cutting from concept to finished product requires an understanding of CAD/CAM design, engineering principles, and material properties. With its accuracy, flexibility, speed, scalability, affordability, and environmental friendliness; laser cutting is quickly becoming an invaluable asset in many industries ranging from aerospace to medical device manufacturing.
Furthermore, with advancements in software capabilities as well as hardware performance; laser cutters can now be used to create complex geometries with detailed results every time.